Liquid Nitriding / Salt Bath Nitriding (SBN) / QPQ / Ferritic Nitro-Carburizing (FNC)
Liquid nitriding is a surface enhancement process with one of the longest track records of success of any ‘case hardening’ technology. It is widely used to cost effectively enhance the wear and corrosion resistance of plain carbon steels, low alloy steels, and stainless steels for a diverse range of precision components and industries, including automotive; oil & gas; hydraulic and pneumatic machinery; firearms; metal forming and forging tools; construction, transportation and material handling equipment, and general purpose industrial machinery.
HEF Group is a pioneer of Liquid Nitriding technology – with over 50 facilities globally offering this versatile surface treatment option. HEF not only provides customized Liquid Nitriding jobbing services globally, but also manufactures the associated, ecologically friendly, nitriding chemicals; and fully instrumented, computer-controlled nitriding lines. This vertically integrated approach provides HEF with the capability to provide a diverse and customized range of liquid nitriding solutions to industrial and automotive customers in 20 countries around the globe. Please contact us at sales@hefusa.net or (937) 323-2556 for all your Liquid Nitriding / Salt Bath Nitriding (SBN) / QPQ / Ferritic Nitro-Carburizing (FNC) needs.
Process Overview
In a liquid nitriding bath, which is maintained between 500 - 630°C (930 - 1165°F), nitrogen-bearing salts produce a controlled and highly uniform release of nitrogen at the surface of the workpiece. Nitrogen diffuses into, and chemically combines with, nitride-forming elements in the metal, producing, through a catalytic reaction, a tough, ductile compound layer with exceptional mechanical properties. This hard compound layer has wear properties that are 200% to 1000% greater than the original material, and greatly enhanced resistance to corrosion, galling and scuffing.
Below the compound zone is another distinctive region, the diffusion zone. This zone results from the progressive diffusion of nitrogen and the formation of a solid solution of nitrogen in the base material. The diffusion zone contributes a critical fourth benefit of salt bath nitriding: substantial enhancement of fatigue strength, typically 20% to 100%.
After Nitriding, the surface can be oxidized to create a 1-3 μm corrosion resistant, black iron-oxide layer
Oxidized Sub-Micron Porosity
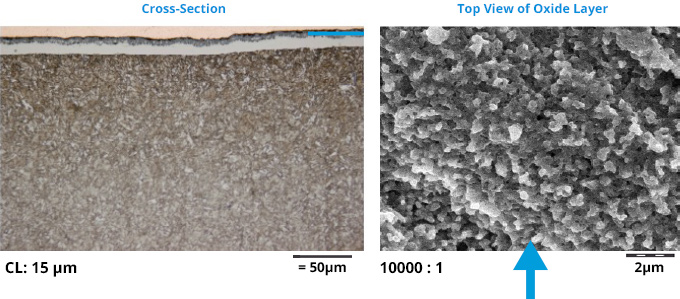
Sub-micron size surface porosity:
- Can be tailored for specific applications
- Very useful for impregnating with especially formulated oils & polymers → significant improvement in corrosion protection & run-in characteristics
- Porosity needs to be controlled – excessive amounts can make compound layer friable
Liquid Nitriding Modifies the Surface Metallurgy and Properties of Ferrous Materials
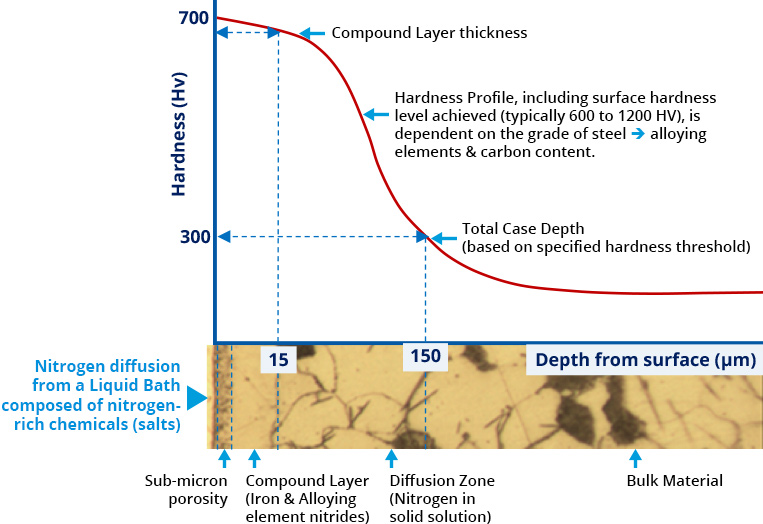